Hello Gray Ghost Fans!
Hard to believe it, but today is Labor Day, the unofficial end of summer! Time to get to work! But wait, I've been at work all summer long! Granted, only during limited morning hours. We all know that I'm a fair weather worker...but I'm good with that. Even with limited morning hours, I've managed to get some solid progress made. As I mentioned in my last post, I wanted to learn how to weld. This is necessary for me to learn, so that I don't have to pay someone else to weld in my patch panels. Those patch panels are being added to replace the rusty (and I do mean rusty) areas in the cab. So, I broke out the old flux core mig welder, bought some weldable sheets of steel and got on it.
Surprise, surprise, welding is not an intuitive skill! I watched a bunch of online videos and read some how to articles. To the surprise of no one, it still takes a lot of practice. To set up the following pics, what I'm doing is to cut a small piece of steel and add a flange to one end. To that end, I also add several 3/8" holes that are meant to replicate the holes that are made when I cut out spot welds. I then attach a 2nd piece of steel under the first with sheet metal screws. This is to hold the two pieces together while I try to weld them. Here's what it looks like:
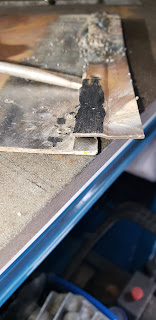 |
First try at welding |
Here, you can see the flange and both pieces of steel. In the background, you can see tons of splatter.... Splatter is common with flux core welding. To me, it's no big deal. It just means some extra grinding to get everything smooth. Onward and upward.... Here's another shot showing progress!
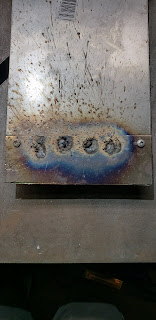 |
Front of practice piece |
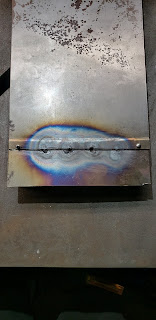 |
Back of practice piece |
Wow! Looks like good penetration of the weld! Now what? Time to put it in a vise and see if a ball peen hammer will bend the metal or break the welds! Well...they broke. That means that the weld penetration wasn't as good as it seemed. Back to the drawing board. The online research on how to weld included stuff about my welder. Nope, not a top of the line welder. One common "upgrade" was to change out the welding wire that came with the welder and get a name brand. I fought that suggestion as long as I could. Feeling like I was up against a wall and not making progress, I broke down and bought name brand wire. Keeping things honest, here, what a difference the new wire made! It burned way hotter and struck the arc before touching the metal. The old wire had to physically touch the metal to strike the arc. This new found capability did require upgrading my welding helmet from permanent dark to auto darkening. The reason was that I got light zapped twice trying to get the electrode close to the metal. The auto darkening helmet takes away that chance. Since then, I've been practicing welding the worst of the worst pieces of metal that I have. Reattaching old pieces to other old pieces. I've had some success, some fails. All in all, though, I think I'm making progress. I have two new pieces of metal in the garage. My plan is to do a real test with good metal and see if the resulting welds can now withstand the ball peen hammer test.
While all that was going on, I was also taking some time to start the actual sheet metal work! I decided to start on the passenger side of the truck, as that side had sunk and the whole cab leaned to the right. After thinking about it (a lot) and talking to my friends on the truck forum, I decided to start with the rocker panel. The reason for starting here is that the rocker panel fits into a channel stamped into the floor pan. On top of the floor pan sits a trim piece. All three pieces have the screw holes in them to accommodate the screws that hold the trim piece to the floor pan. Those screw holes all have to line up, so they are the landmarks that I was looking for. Everything else will key off of the rocker panel and the rocker panel will key off of the floor pan screw holes. At least, that's my plan. Here's a pic of the old rocker panel with the bottom of the hinge pillar still attached:
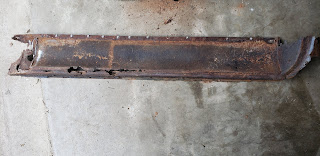 |
Old rocker panel |
And the spot that is now open:
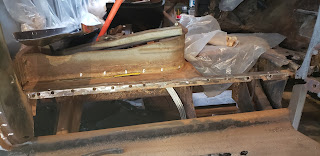 |
Space for new rocker panel |
The holes from drilling out the spot welds are clearly visible. The white hash marks on the lock pillar and the seat riser are where other spot welds are located. The seat riser spot welds will not be drilled out. The ones on the lock pillar will be drilled out as that is the end of the cab corner, which will get replaced. Here's a pic of the new rocker panel being test fit into the opening.
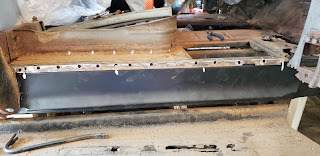 |
New rocker test fit |
The white hash marks on the new rocker panel align with the screw holes. I used them as a guide for setting the rocker panel in the correct place. To the right you can see where the missing hinge pillar used to be.... So, with the test fit a success, I removed the rocker panel so I could have easy access to the cab mount and cab corners.
As I mentioned above, the cab leaned to the right. To start to rectify this, I used factory holes in the firewall and mounted a piece of 1x4 to the cab. I then used the floor jack and raised the cab until the gap between the frame rail and floor board was at the specified height, which was 1.78 inches. Here's a pic before raising the cab:
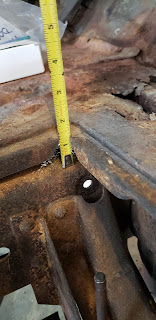 |
Floor height measurement |
If you zoom the pic, you can see that it's between 1.25 and 1.5 inches. Once I got it withing range, I used scrap 2x4's attached to the 1x4 to brace the cab in the correct position. Then, I used the floor jack and more scrap wood to raise up the rear of the cab. Once the rear was correctly raised, I used a 2x6 scrap to hold the rear of the cab in place. Now it was time to remove the "body mounting shackle", better known as the rear cab mount. Here is what it looked like on the workbench:
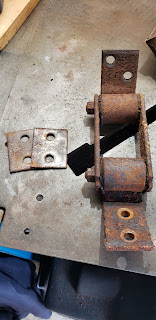 |
Body mounting shackle |
The two pieces on the left are shims installed by the factory. They'll get cleaned and reused. Disassembled, the shackle parts looked like this:
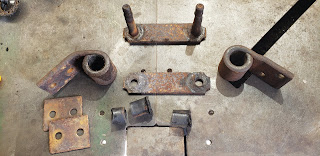 |
Disassembled shackle |
Once the shackle was disassembled, it was obvious that the shackle bolts had to be replaced. There were press fit into the shackle side bar. I was able to knock them out and replace them with new shoulder bolts of the correct diameter and length. Here is the comparison:
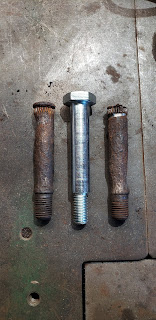 |
Shoulder bolts |
After disassembly, it was back to the old refurbishment process of removing the flaky scale, spraying with the Rustoleum Rust Reformer and Rustoleum Satin Black. After restoration, the parts looked like this:
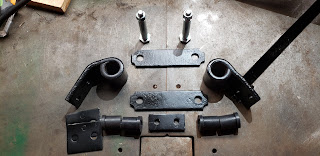 |
Restored shackle parts + replacement parts |
Once it was reassembled, it looked like this:
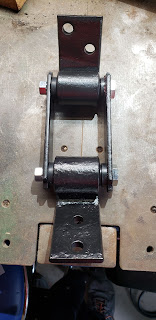 |
Restored shackle |
At that point, it was time to reinstall it on the truck. That looked like this:
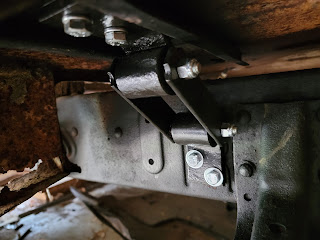 |
Restored shackle installed on truck |
While I was there, I took the time to spray the frame section that was exposed. It got the same Rust Reformer and Satin Black treatment. It's not as good as doing the whole frame, all at once, but I'm not doing a concourse restoration. In fact, I'm thinking about clear coating the exterior of the truck to preserve the "patina". We'll see.... Here's another pic of the shackle before restoration. In this shot, I've removed one shackle side and you can see the rubber bushings installed in the brackets, with the bolts protruding. This shot shows you just how nasty the shackle truly was:
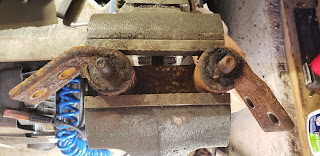 |
Unrestored shackle |
Once the shackle was reinstalled, the brace in the rear was removed and the cab sat perfectly level and at the correct height. That's a win in my book!
So, this catches you up and brings me to the end of summer/beginning of fall. This is prime time for working on the truck and my first fall in retirement. I'm hoping to spend a lot of time in the garage!
I'm also writing a journal on the
https://www.stovebolt.com/ . The journal is where I'm writing about the detailed, day to day progress on this phase of the restoration. If you are interested in the daily goings on, then I'd encourage you to visit the site and follow along. If you like working on old Chevy trucks, then this is the place to go!
That's all for now! Thanks for reading!