As I mentioned in my last post, I wanted to do the rewiring / restoration of the remaining backup light (the Guide Lamp Company B-31) this weekend. Before I got to the light, I had an idea of making a bracket similar to ones that I had seen on eBay for these backup lights. They looked pretty straightforward, essentially just an L shaped piece of flat steel with a smaller flat steel piece that went on the opposite side of the bumper bracket. They were held together with small bolts and nuts. Like I said seemed pretty straightforward. But the reality was not so much. I got the flat stock, made the measurements and made my first bend. So far so good. But when I got it to the truck, I realized that the geometry of the bumper brackets (not right angles to the bumper) would require something that would pivot. I had seen those, too, on eBay, but didn't want to spend the money to get them. Guess what...I'll be getting them. After making a valiant attempt at making my original idea work, I had to give up. Wasn't going to happen. So I'll be saving my money to buy the brackets online. In the meantime, I went back to the B-31.
Disassembly was easy and the major parts looked like this when apart:
and this:
The black gunk in both pics are the remnants of the original gasket. Not sure what they made it out of, but it came out in big hunks. What remained came out with Formula 409 on a paper towel and some wiping.
You'll notice some rusting on the bulb housing, just like in the previous light. The difference here, is that this light still has the original carriage bolt attached and it is press fit into the housing. So it wasn't going to go anywhere. That meant that I would have to remove the rust with the bulb housing still attached to the light housing or body. That made things difficult. After I was done, I was pretty happy with the rust removal, but decided that I would not paint the bulb housing like I did on the previous light. I really didn't want to go through the masking of the interior of the housing and trying to shoot spray paint down the small opening of the light housing onto the bulb housing. I guess that I could have done it, but likely with some mess to clean up.
Anyway, after that decision, all that was left was to trim down the bulb holder so that it fit and run the wires. The trimming was just like the last one, so no problems there. However, because the bulb holder was still attached to the light housing, I had to fish the wires through the bottom of the bulb holder and over to the light housing exit. At first, I wanted to keep the original grommet in place, but the hole is small and using another piece of wire for fishing meant that I was going to try to get 3 pieces of wire through a grommet meant for 1 wire. Wasn't going to work. So out came the grommet and fortunately, it came out in one piece and was kind of pliable. After that, fishing the light socket wires was straightforward. Especially when I used my hooked pick to snag the wires from behind the light bulb holder and bring them to the exit. After the wires were out, I reinstalled the grommet. Here is a shot of the major components after cleaning and with the new socket, wires and LED bulb installed. You can see the old wire harness in the foreground and it is clear why I needed to replace it.
Then it was off to make another gasket. I used the lens cover and the lens as templates for the new gasket. The next pic shows the stages of cutting the gasket and the tools to do so.
Basically the stages are:
1. Cut out a chunk of bicycle inner tube big enough to make the gasket and then cut it down the middle to make a square.
2. Using the glass lens as a template, mark the outer dimension of the gasket and cut out the circle. I used the trimmers to cut out the circle.
3. Then put the circle into the lens cover and put the glass lens into the cover, but put it in backwards. That way you can mark the rubber circle for the inside ring, using the lens cover. I first used the box cutter to trace the outline of the inner circle. Once I had gone around the circle a couple of times, the box cutter broke through in one place. Then I used the trimmers to cut out the remaining parts of the circle.
4. Put the gasket back into the lens cover and mark the opening for the drain hole. I used small scissors to cut this out.
The test fit after all the cutting looked like this:
Here it is with the glass lens installed and the attaching screw through the hole.
After all of that, it was time to put the lens and cover back onto the light. When reassembled, it looked like this:
You can see that there is some minor corrosion on the original carriage bolt. I'll deal with that later. I did do a test of the light to make sure it works, which it did, but I did not take a pic. Kinda looks like the first one, although you can see the difference in the glass lens. This one has the "beehive" lens and the BLC light has the "bomber" lens. Both look good and unless you are right up on them, you could never tell the difference. Personally, I like the difference.
Stay tuned for the next update. I hope to work on the 3rd brake light next. It is not an ordinary light and I'm excited to do the minor fixup necessary to make it work and hold up to the weather.
OBTW, Happy Thanksgiving, Everyone!
All about working on and restoring my 1953 Chevy 3100 (1/2 ton) pickup truck including the inline 6 235 engine
1953 chevy truck ad
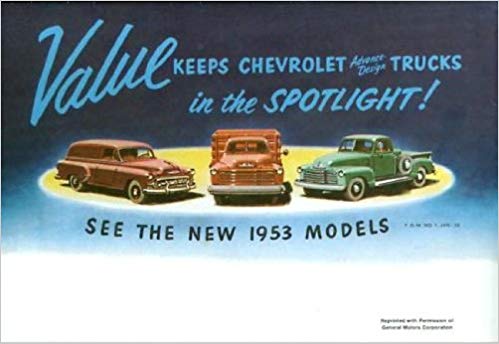
Thursday, November 26, 2015
Sunday, November 22, 2015
Backup! Lights....
Back up lights were not available for 1953 trucks at all. Neither as standard equipment nor as a factory option. Some people added them as aftermarket items, but most people didn't bother. I wanted them for my truck and I have a few spare circuits on my new wiring harness, so I thought I'd look around to see what was out there. After searching around online, I decided to go with the Guide Lamp Company (GM's light supplier) B-31 lamps. They are a teardrop shape with chrome plating on the outside and a clear glass lens. I found an ebay auction that had 1 B-31 and 1 BLC B-M4 lamp. The BLC lamp is very similar to the B-31, just a little smaller and with a different pattern in the clear glass lens. Being from the 1940's - 1950's, I figured I'd have to do some clean up and re-wiring to make them suitable for use. I also wanted to upgrade to LED bulbs. I wanted the LED bulbs because they tend to be brighter and they have virtually no current draw.
When I got the lamps, I noticed that the BLC lamp had a split in the chrome body that I had not noticed in the auction. I decided to start the restoration on this one, since it was already damaged and would make a good learning piece. Here's how it went....
When I got the lamp in the mail and inspected it, I noticed the split. When I took the lens and cover off, the split looked like this:
It is a pretty big split, running from the lip about an inch and a half. The metal was too thin for me to try and weld up the split, so I decided to try to save the housing using some JB Weld. I put the JB Weld in the inside of the housing, forcing some down into the split. It looked like this when dry:
Nothing fancy here, just really strong epoxy. I'm hopeful that it, combined with the lens cover, will hold the split from advancing any further.
Next, I turned my attention to the bulb holder assembly. The original 6v bulb had corroded in the holder, plus there was some surface corrosion on all parts of the holder. To clean this up, I used the Dremel tool with a mildly abrasive wheel. It took it right off and had the added benefit of fitting down inside where the bulb sits. The bulb was a single contact bayonet style bulb and was the same size as the modern 1156 size bulb. The single contact bayonet style bulb gets current through the single contact and grounds through contact with the side of the bulb holder, which in turn must ground through the chassis or frame. Since these backup lights were going to be mounted onto the pretty rusty bumper brackets, it was going to be difficult to get a good ground there. So, I decided that I wanted to switch to a bulb socket that would use 2 contacts instead of 1. Unfortunately, with this style of bulb holder, 2 contacts means 2 positive contacts, not a positive and negative. These would be used for brake lights, where you need a low and high and you would use a double filament bulb. Not what I needed.
I did some research and found that the more recent side marker light used 2 contacts (both positive and negative). The drawback was that they were designed to snap into the side marker housing and lock in place with a twist, not sit in the can that was used for my bulbs. However, they were close in size and I figured that I could trim them down a bit and then they'd fit. Here's a shot of a trimmed socket and an untrimmed socket for comparison:
It may be a little hard to tell in this shot, but the bottom one is trimmed and the top one is original size. I used the Dremel tool here, too and just took my time and test fit it repeatedly until I got it just right. It was a snug fit, but the cup near the bulb sits right in the top of the old bulb can and looks like it was meant to be there. Here's a shot of the bulb socket and pigtail being test fit in the housing:
In this shot you can see that after I took care of the corrosion on the bulb holder I went ahead and painted it. Since I no longer needed metal to metal contact for the ground connection, there was no need to leave it bare metal, especially since it had already corroded once. A coat of Rustoleum Automotive Primer and Valspar Satin Black took care of the job nicely. In this shot, you can see the screw hole for the lens cover to attach to the housing. The bulb holder assembly is mounted to the housing through a 1/4" carriage bolt that will also secure the lamp to whatever bracket I end up getting to mount the lights to the truck.
Here is an exploded view of all the parts, numbered, so that I can label them for the reader:
1. Lens Cover
2. Lens Cover Mounting Screw
3. Glass Lens
4. Home Made Rubber Gasket
5. Socket Pigtail
6. Stainless Steel Carriage Bolt, Washer, Nut, Lock Washer and Lock Nut
7. Light Socket Holder
8. Original Grommet
9. Lamp Housing
I made the gasket out of an old bicycle inner tube. I used the glass lens as a template and cut out for the drainage hole that is at the bottom of the light. I reused the original grommet. It was kind of hard, so I heated it up with an old hair dryer to soften up the rubber a bit and managed to work it back into place. The grommet and pigtail exit looked like this:
After assembly, I took it into the garage and did a quick test by touching the wires to a battery. It looked like this:
Yay, light!
All in all not bad, as long as the JB Weld holds. We'll see. Not a difficult project, but one I wanted to get done. I've still got the B-31 left to do and will tackle that next weekend sometime. I also bought a light that I'm going to use as a 3rd brake light...but that will be the subject of a separate post.
When I got the lamps, I noticed that the BLC lamp had a split in the chrome body that I had not noticed in the auction. I decided to start the restoration on this one, since it was already damaged and would make a good learning piece. Here's how it went....
When I got the lamp in the mail and inspected it, I noticed the split. When I took the lens and cover off, the split looked like this:
It is a pretty big split, running from the lip about an inch and a half. The metal was too thin for me to try and weld up the split, so I decided to try to save the housing using some JB Weld. I put the JB Weld in the inside of the housing, forcing some down into the split. It looked like this when dry:
Nothing fancy here, just really strong epoxy. I'm hopeful that it, combined with the lens cover, will hold the split from advancing any further.
Next, I turned my attention to the bulb holder assembly. The original 6v bulb had corroded in the holder, plus there was some surface corrosion on all parts of the holder. To clean this up, I used the Dremel tool with a mildly abrasive wheel. It took it right off and had the added benefit of fitting down inside where the bulb sits. The bulb was a single contact bayonet style bulb and was the same size as the modern 1156 size bulb. The single contact bayonet style bulb gets current through the single contact and grounds through contact with the side of the bulb holder, which in turn must ground through the chassis or frame. Since these backup lights were going to be mounted onto the pretty rusty bumper brackets, it was going to be difficult to get a good ground there. So, I decided that I wanted to switch to a bulb socket that would use 2 contacts instead of 1. Unfortunately, with this style of bulb holder, 2 contacts means 2 positive contacts, not a positive and negative. These would be used for brake lights, where you need a low and high and you would use a double filament bulb. Not what I needed.
I did some research and found that the more recent side marker light used 2 contacts (both positive and negative). The drawback was that they were designed to snap into the side marker housing and lock in place with a twist, not sit in the can that was used for my bulbs. However, they were close in size and I figured that I could trim them down a bit and then they'd fit. Here's a shot of a trimmed socket and an untrimmed socket for comparison:
It may be a little hard to tell in this shot, but the bottom one is trimmed and the top one is original size. I used the Dremel tool here, too and just took my time and test fit it repeatedly until I got it just right. It was a snug fit, but the cup near the bulb sits right in the top of the old bulb can and looks like it was meant to be there. Here's a shot of the bulb socket and pigtail being test fit in the housing:
In this shot you can see that after I took care of the corrosion on the bulb holder I went ahead and painted it. Since I no longer needed metal to metal contact for the ground connection, there was no need to leave it bare metal, especially since it had already corroded once. A coat of Rustoleum Automotive Primer and Valspar Satin Black took care of the job nicely. In this shot, you can see the screw hole for the lens cover to attach to the housing. The bulb holder assembly is mounted to the housing through a 1/4" carriage bolt that will also secure the lamp to whatever bracket I end up getting to mount the lights to the truck.
Here is an exploded view of all the parts, numbered, so that I can label them for the reader:
1. Lens Cover
2. Lens Cover Mounting Screw
3. Glass Lens
4. Home Made Rubber Gasket
5. Socket Pigtail
6. Stainless Steel Carriage Bolt, Washer, Nut, Lock Washer and Lock Nut
7. Light Socket Holder
8. Original Grommet
9. Lamp Housing
I made the gasket out of an old bicycle inner tube. I used the glass lens as a template and cut out for the drainage hole that is at the bottom of the light. I reused the original grommet. It was kind of hard, so I heated it up with an old hair dryer to soften up the rubber a bit and managed to work it back into place. The grommet and pigtail exit looked like this:
After assembly, I took it into the garage and did a quick test by touching the wires to a battery. It looked like this:
Yay, light!
All in all not bad, as long as the JB Weld holds. We'll see. Not a difficult project, but one I wanted to get done. I've still got the B-31 left to do and will tackle that next weekend sometime. I also bought a light that I'm going to use as a 3rd brake light...but that will be the subject of a separate post.
Saturday, November 21, 2015
To The Basement Of The GM Science Building!
A quick post to let everyone know that I've added a link to the GM Heritage Center for the 1953 Chevrolet Truck. The link is on the Technical Information page, at the top. The link opens the official Chevrolet Vehicle Information Kit for the 1953 truck and includes tons of useful information. If you work backwards, you can also find links to most of their other vehicles and years. Enjoy!
Saturday, November 7, 2015
Rusty Mouse Pee and a Stinky Cab
Yesterday was a very long, but very productive day in the garage. Eight hours worth, to be exact. During that time, I got the truck down off of the jack stands and out into the driveway. That was the first time that the truck had been outside of the garage in 5 years! The point of getting it out of the garage was to completely scrub the interior to get rid of the mouse droppings/pee and the attendant smell. Once I got it off of the stands, I had my helper get into the cab to work the newly refurbished brakes, while I pushed it out. Before putting our full faith in my brake rebuild, I had my helper test them out by pressing on the brake pedal while I tried to push. The first attempt was a false start, as I had forgotten to take it out of 1st gear. After figuring that out, we tried again. Brake pedal pushed, truck pushed and no movement! They were holding! Next it was release the brake pedal, start rolling backwards and engage the pedal again. The truck instantly stopped! Repeat several more times until the entire cab was outside. Chocked all 4 wheels, put the truck back into first gear and she wasn't going to roll anywhere.
Before I could scrub anything, I had to make sure the cab was stripped of everything. That was the purpose of removing the gauge clusters last weekend. This time I started with the seat cushions and just put them into the garage for later that day. Once the cushions were out, I took out the seat frame and put it in the yard for a good scrub with a water/soap/bleach solution and a good scrub brush. After the scrub, it got a good rinse with plain water and put into the sun to dry. Next it was time to take the primary offender out...the gas tank. The tank was the primary offender because there was a mouse dropping/pee sludge on top of the tank, down the side of the tank and under the tank. The only way to get it all out was to remove the tank. I made an effort to remove the clutch head screws that held the sending unit wires to the sending unit, but somehow lost the size 1 clutch head bit. So...time for the wire cutters. It really didn't make any difference, since I do not plan to reuse the wires. After that I had to loosen the hold down straps and then the tank came right out. Here are a series of pics showing the cab before cleaning:
To get a sense of just how dirty the cab floor, especially under where the tank used to be, is to click on the pic and enlarge it. You'll see a flaky crud that is the mix of rust, droppings and pee that has dried up over the years. It would always smell like pee whenever it was humid outside. I used the same combo of water, soap and bleach to scrub out the entire cab. I started with the roof of the cab and worked my way down the sides doing all surfaces including the dash and doors. I would do a little and then rinse. After I was done, I took the leaf blower to the water puddles that were inside the cab. Blew them right out! I propped open the doors and let the nice breeze blow through the truck to dry it out. While I was waiting for the inside to dry, I went back in the garage and stripped the old upholstery off of the seat back and bottom cushions. It was gnarly! I did find a nice, neat 1" diameter hole in the material where a little field mouse had gnawed a hole through and got his nest material.... Once the frames were stripped, they got the same treatment. Scrubbed and rinsed and set out in the yard to dry.
After drying the inside of the cab looked like this:
You can see that the pile of crud is gone. You can also see the remnants of body sealer that the factory used to seal the seat apron joint to the cab floor. Everything had a nice bleach smell. A dramatic improvement!
Once the frames were dry, I simply oiled the seat adjustment rails, reattached the seat frame and bolted it down. Then I set the seat cushion frames back into place and called for my helper. With the help of a 3rd helper, we pushed the truck back into the garage and chocked the wheels. She is now ready for a long winter of rewiring, gauge cluster refurbishment and the beginnings of removing bits from the installed engine in preparation for the engine swap next spring.
As a side note, in order to get the gas tank out, I first had to remove the petcock that was attached to the bottom of the tank. I actually did that before getting the truck down off of the jack stands. It was funny because when I got the petcock off of the pipe nipple I could see that the pipe nipple was completely blocked with dried mud. It was interesting, but I didn't really think about it until I was moving the tank into the back yard. When I was moving it, I could hear dried mud sliding around in the tank. I didn't check to see exactly how much dirt and debris was actually in the tank, but it seems likely that I'll end up replacing the tank instead of reusing it, unless I can find someone to boil it out and it turns out to be free of holes.
All in all, it was a lot of work and a very long day, boiled down into a couple of paragraphs. By the end of the day, I was exhausted and very sore, but it was likely the last 80 degree day and I knew I had to get it done, so I did.
Oh yeah, and I only got stung by 1 bee while I was working. I don't know what the yellow jackets like about the smell of the Kroil, but it makes them come buzzing around and 1 of them decided that I needed to be stung. Go figure.
Before I could scrub anything, I had to make sure the cab was stripped of everything. That was the purpose of removing the gauge clusters last weekend. This time I started with the seat cushions and just put them into the garage for later that day. Once the cushions were out, I took out the seat frame and put it in the yard for a good scrub with a water/soap/bleach solution and a good scrub brush. After the scrub, it got a good rinse with plain water and put into the sun to dry. Next it was time to take the primary offender out...the gas tank. The tank was the primary offender because there was a mouse dropping/pee sludge on top of the tank, down the side of the tank and under the tank. The only way to get it all out was to remove the tank. I made an effort to remove the clutch head screws that held the sending unit wires to the sending unit, but somehow lost the size 1 clutch head bit. So...time for the wire cutters. It really didn't make any difference, since I do not plan to reuse the wires. After that I had to loosen the hold down straps and then the tank came right out. Here are a series of pics showing the cab before cleaning:
To get a sense of just how dirty the cab floor, especially under where the tank used to be, is to click on the pic and enlarge it. You'll see a flaky crud that is the mix of rust, droppings and pee that has dried up over the years. It would always smell like pee whenever it was humid outside. I used the same combo of water, soap and bleach to scrub out the entire cab. I started with the roof of the cab and worked my way down the sides doing all surfaces including the dash and doors. I would do a little and then rinse. After I was done, I took the leaf blower to the water puddles that were inside the cab. Blew them right out! I propped open the doors and let the nice breeze blow through the truck to dry it out. While I was waiting for the inside to dry, I went back in the garage and stripped the old upholstery off of the seat back and bottom cushions. It was gnarly! I did find a nice, neat 1" diameter hole in the material where a little field mouse had gnawed a hole through and got his nest material.... Once the frames were stripped, they got the same treatment. Scrubbed and rinsed and set out in the yard to dry.
After drying the inside of the cab looked like this:
You can see that the pile of crud is gone. You can also see the remnants of body sealer that the factory used to seal the seat apron joint to the cab floor. Everything had a nice bleach smell. A dramatic improvement!
Once the frames were dry, I simply oiled the seat adjustment rails, reattached the seat frame and bolted it down. Then I set the seat cushion frames back into place and called for my helper. With the help of a 3rd helper, we pushed the truck back into the garage and chocked the wheels. She is now ready for a long winter of rewiring, gauge cluster refurbishment and the beginnings of removing bits from the installed engine in preparation for the engine swap next spring.
As a side note, in order to get the gas tank out, I first had to remove the petcock that was attached to the bottom of the tank. I actually did that before getting the truck down off of the jack stands. It was funny because when I got the petcock off of the pipe nipple I could see that the pipe nipple was completely blocked with dried mud. It was interesting, but I didn't really think about it until I was moving the tank into the back yard. When I was moving it, I could hear dried mud sliding around in the tank. I didn't check to see exactly how much dirt and debris was actually in the tank, but it seems likely that I'll end up replacing the tank instead of reusing it, unless I can find someone to boil it out and it turns out to be free of holes.
All in all, it was a lot of work and a very long day, boiled down into a couple of paragraphs. By the end of the day, I was exhausted and very sore, but it was likely the last 80 degree day and I knew I had to get it done, so I did.
Oh yeah, and I only got stung by 1 bee while I was working. I don't know what the yellow jackets like about the smell of the Kroil, but it makes them come buzzing around and 1 of them decided that I needed to be stung. Go figure.
Sunday, November 1, 2015
The Bleeding Has Stopped!
Yesterday was a very productive day in the garage. It was a long day, but a productive day. I started out determined to use the new brake adjustment tool (officially called a brake spoon) to adjust the brake shoes. Once that was done, I could move back to bleeding the brakes. As you may recall, I got as far in the process of loosening all 4 anchor pin nuts and actually adjusting the brake shoes on 1 wheel. Then I found out that I needed the brake spoon to make the final adjustment. During the week, I went to the FLAPS and got the tool. Yesterday, I got under the truck and found that the tool worked wonderfully well! Armed with this new tool, I set out to do the remaining 3 wheels. It actually went very quickly and I was very happy with the results. Then it was back to bleeding the brakes.
For this effort, I had no helper. It was just me, an empty soda bottle with a hole drilled in the cap and a clear, flexible hose. This turned out to be pretty simple, too. I was very cautious to make sure that I didn't drain the master cylinder and reintroduce air into the brake lines, constantly going from the master cylinder, to the wheel being bled and back again. Each time pumping the brake pedal and then checking to see if fluid or bubbles could be seen. Once I was satisfied that the line was clear, I tightened the bleed valve and was off to the next wheel. The sequence, according to the shop manual, is: left rear, right rear, right front and left front. This takes you from the farthest point from the master cylinder to the closest. Once all 4 wheels had been bled, it was time to fill the master cylinder, put the cap back on and pump the pedal! VOILA! It works! I got steady pedal pressure.
After getting steady pressure, I went back under the truck to check for leaks and found 2 small ones. One leak was at the rear junction block where the hard line is split between left and right wheels. The other was at the master cylinder where the separate hard line joins the junction block to go to the left front wheel. Using the correct line wrench (a flare nut wrench), I flanged down on both offenders and problem solved.
Feeling pretty good about things, I decided to start in on stripping the interior of things that I didn't want ruined when I scrub out the interior. I need to scrub out the interior, because mice had lived in the truck when it was out in the field and the inside smells of mouse pee! So, knowing that I will want to save the gauges, I decided to start there.
It was very difficult to reach the nuts that hold the speedometer and gauge cluster to the dash, as they are true blind connections. After fiddling with wrenches, sockets, etc, I was finally able to remove both parts to the gauge cluster. The looked like this when out of the truck:
Here's a closeup of the speedometer/odometer:
Here's a closeup of the gauge cluster:
Here's a shot of the backs of the gauges:
And here is the money shot, an extreme closeup of the odometer where you can actually make out the original miles on the truck (61590.?):
Even enlarging the pic or looking under really bright lights, I could not figure out the tenths of a mile number. I guess I'll have to wait until I drive it and it rolls to the next digit, which won't be faded. Then I'll know.
So now that the gauges are out, I have to remove the seat and frame so that I can get to the gas tank. The tank needs to come out, as that is where a lot of the crud still remains inside the truck. Once those are out, I plan to scrub the interior with bleach/water and then rinse it out. Afterwards, I can refurbish the gas tank and reinstall, then refurbish the seat and frame and then the gauges. Then I can set about removing the old wire harness and installing the new wire harness. Then, it is time to think about getting the old tranny out and transferred to the replacement engine.... But, one step at a time.
For this effort, I had no helper. It was just me, an empty soda bottle with a hole drilled in the cap and a clear, flexible hose. This turned out to be pretty simple, too. I was very cautious to make sure that I didn't drain the master cylinder and reintroduce air into the brake lines, constantly going from the master cylinder, to the wheel being bled and back again. Each time pumping the brake pedal and then checking to see if fluid or bubbles could be seen. Once I was satisfied that the line was clear, I tightened the bleed valve and was off to the next wheel. The sequence, according to the shop manual, is: left rear, right rear, right front and left front. This takes you from the farthest point from the master cylinder to the closest. Once all 4 wheels had been bled, it was time to fill the master cylinder, put the cap back on and pump the pedal! VOILA! It works! I got steady pedal pressure.
After getting steady pressure, I went back under the truck to check for leaks and found 2 small ones. One leak was at the rear junction block where the hard line is split between left and right wheels. The other was at the master cylinder where the separate hard line joins the junction block to go to the left front wheel. Using the correct line wrench (a flare nut wrench), I flanged down on both offenders and problem solved.
Feeling pretty good about things, I decided to start in on stripping the interior of things that I didn't want ruined when I scrub out the interior. I need to scrub out the interior, because mice had lived in the truck when it was out in the field and the inside smells of mouse pee! So, knowing that I will want to save the gauges, I decided to start there.
It was very difficult to reach the nuts that hold the speedometer and gauge cluster to the dash, as they are true blind connections. After fiddling with wrenches, sockets, etc, I was finally able to remove both parts to the gauge cluster. The looked like this when out of the truck:
Here's a closeup of the speedometer/odometer:
Here's a closeup of the gauge cluster:
Here's a shot of the backs of the gauges:
And here is the money shot, an extreme closeup of the odometer where you can actually make out the original miles on the truck (61590.?):
Even enlarging the pic or looking under really bright lights, I could not figure out the tenths of a mile number. I guess I'll have to wait until I drive it and it rolls to the next digit, which won't be faded. Then I'll know.
So now that the gauges are out, I have to remove the seat and frame so that I can get to the gas tank. The tank needs to come out, as that is where a lot of the crud still remains inside the truck. Once those are out, I plan to scrub the interior with bleach/water and then rinse it out. Afterwards, I can refurbish the gas tank and reinstall, then refurbish the seat and frame and then the gauges. Then I can set about removing the old wire harness and installing the new wire harness. Then, it is time to think about getting the old tranny out and transferred to the replacement engine.... But, one step at a time.
Subscribe to:
Posts (Atom)